Technological innovation of clean smelting in electric arc furnace
Crushing and separation technology of scrap steel.
Scrap steel is a superior recycling resource for iron and steel recycling. The resource utilization of scrap steel plays an important role in energy saving, emission reduction, transformation and upgrading of iron and steel industry. High-efficiency crushing and separation of scrap steel is the premise and key to ensure the quality of raw materials for EAF steelmaking, and it is very important to realize clean smelting in EAF steelmaking.
There are two kinds of scrap crusher: scrap crusher and crusher. The crusher is used to crush steel scraps, and the crusher is used to crush large scrap steel. Crusher has hammer type, roll type and blade type. Waste steel after crushing can be easily separated and recycled by dry, wet or semi-wet sorting system for metal, non-metal, non-ferrous metal and ferrous metal. Paint and coating on the surface of waste steel can be removed or partially removed. The scrap after crushing and sorting can greatly improve the cleanliness of raw materials and provide a clean and reliable raw material guarantee for EAF steelmaking.
Compound blowing technology for electric arc furnace steelmaking.
Traditional electric arc furnace steelmaking pool stirring intensity is weak, which inhibits the transfer of material and energy in the furnace. Ultra-high power power supply and high-strength chemical energy input are usually used, but the problems such as insufficient stirring intensity in the pool and slow transfer of material and energy are not fundamentally solved. Oxygen blowing process is widely used in modern EAF steelmaking to speed up smelting rhythm and reduce production costs. Several enhanced oxygen supply technologies, such as wall oxygen supply, door oxygen supply and cluster jet, have been developed successively. In order to solve the problems of insufficient stirring intensity in molten pool and slow transfer of material and energy, key technologies such as bottom blowing stirring and composite blowing in electric arc furnace steelmaking have been developed.
Aiming at high efficiency, low consumption, energy saving and high quality production, the research team of Peking University of Science and Technology first proposed and developed a new generation of electric arc furnace smelting technology-composite blowing technology for electric arc furnace steelmaking (see attached figure). With new technologies such as cluster oxygen supply and synchronous long life bottom blowing stirring as the core, electric arc furnace steelmaking power supply, oxygen supply and so on were realized. The operation integration of bottom blowing and other units meets the technical requirements of composite blowing in arc furnace steelmaking under multi-burden conditions.
Cluster modular energy supply technology.
The cluster modular energy supply technology of electric arc furnace includes the cluster oxygen supply mode of furnace wall and furnace top. The oxygen supply and the powder injection unit are installed on the integrated water cooling module of the furnace wall, with the help of melting and decarburization modes. The dynamic switching of gas solid mixing injection, gas powder (carbon powder, dephosphorization agent, etc.) can be realized to meet the requirements of foamed slag, dephosphorization and control of molten steel peroxide. The kinetic energy of the particles can effectively transport oxygen and powder to the slag steel reaction interface, stabilize foam slag, reduce power consumption and increase metal yield. Aiming at the multi-material structure smelting with high iron-water ratio, the team developed oxygen injection technology on the top of electric arc furnace to increase the oxygen supply intensity in the furnace and strengthen the stirring of molten pool. The technology can switch between power supply and oxygen supply, complete decarbonization and dephosphorization smelting tasks, improve oxygen supply efficiency, shorten smelting time and reduce smelting power consumption.
Crushing and separation technology of scrap steel.
Scrap steel is a superior recycling resource for iron and steel recycling. The resource utilization of scrap steel plays an important role in energy saving, emission reduction, transformation and upgrading of iron and steel industry. High-efficiency crushing and separation of scrap steel is the premise and key to ensure the quality of raw materials for EAF steelmaking, and it is very important to realize clean smelting in EAF steelmaking.
There are two kinds of scrap crusher: scrap crusher and crusher. The crusher is used to crush steel scraps, and the crusher is used to crush large scrap steel. Crusher has hammer type, roll type and blade type. Waste steel after crushing can be easily separated and recycled by dry, wet or semi-wet sorting system for metal, non-metal, non-ferrous metal and ferrous metal. Paint and coating on the surface of waste steel can be removed or partially removed. The scrap after crushing and sorting can greatly improve the cleanliness of raw materials and provide a clean and reliable raw material guarantee for EAF steelmaking.
Compound blowing technology for electric arc furnace steelmaking.
Traditional electric arc furnace steelmaking pool stirring intensity is weak, which inhibits the transfer of material and energy in the furnace. Ultra-high power power supply and high-strength chemical energy input are usually used, but the problems such as insufficient stirring intensity in the pool and slow transfer of material and energy are not fundamentally solved. Oxygen blowing process is widely used in modern EAF steelmaking to speed up smelting rhythm and reduce production costs. Several enhanced oxygen supply technologies, such as wall oxygen supply, door oxygen supply and cluster jet, have been developed successively. In order to solve the problems of insufficient stirring intensity in molten pool and slow transfer of material and energy, key technologies such as bottom blowing stirring and composite blowing in electric arc furnace steelmaking have been developed.
Aiming at high efficiency, low consumption, energy saving and high quality production, the research team of Peking University of Science and Technology first proposed and developed a new generation of electric arc furnace smelting technology-composite blowing technology for electric arc furnace steelmaking (see attached figure). With new technologies such as cluster oxygen supply and synchronous long life bottom blowing stirring as the core, electric arc furnace steelmaking power supply, oxygen supply and so on were realized. The operation integration of bottom blowing and other units meets the technical requirements of composite blowing in arc furnace steelmaking under multi-burden conditions.
Cluster modular energy supply technology.
The cluster modular energy supply technology of electric arc furnace includes the cluster oxygen supply mode of furnace wall and furnace top. The oxygen supply and the powder injection unit are installed on the integrated water cooling module of the furnace wall, with the help of melting and decarburization modes. The dynamic switching of gas solid mixing injection, gas powder (carbon powder, dephosphorization agent, etc.) can be realized to meet the requirements of foamed slag, dephosphorization and control of molten steel peroxide. The kinetic energy of the particles can effectively transport oxygen and powder to the slag steel reaction interface, stabilize foam slag, reduce power consumption and increase metal yield. Aiming at the multi-material structure smelting with high iron-water ratio, the team developed oxygen injection technology on the top of electric arc furnace to increase the oxygen supply intensity in the furnace and strengthen the stirring of molten pool. The technology can switch between power supply and oxygen supply, complete decarbonization and dephosphorization smelting tasks, improve oxygen supply efficiency, shorten smelting time and reduce smelting power consumption.
Embedded oxygen injection technology. In recent years, based on the development of multi-functional cluster modular energy supply technology, the team has developed the submerged oxygen injection technology for EAF steelmaking in order to further improve oxygen utilization efficiency and improve the metallurgical reaction kinetics of EAF pool. The technology moves the oxygen supply mode from above the molten pool to below the molten steel level, and injects oxygen directly into the molten pool with a spray gun, thus speeding up the metallurgical reaction and increasing the oxygen utilization rate to 98%. In order to solve the problem of burning and erosion of refractories by oxygen flow in submerged spray gun, the annular cyclone protection technology was adopted, and the erosion rate was controlled by the central main jet "protection-smelting-tapping" control mode, so that the life of spray gun could be synchronized with the furnace life. The technology can remarkably improve the flow and chemical reaction speed of molten steel, effectively control the peroxidation of molten steel and improve the dephosphorization efficiency of molten pool.
Safety and longevity bottom blowing technology for EAF steelmaking.
The metallurgical reaction kinetics of EAF steelmaking pool is poor, the composition and temperature of molten steel in the pool are not uniform, the oxygen content at the end point and the iron oxide content in slag are high, which ultimately affect the smelting index and the quality of molten steel. The safe and long life bottom blowing technology of EAF steelmaking developed by the team strengthens the stirring of EAF melting pool. Oxygen consumption per ton of steel, consumption of iron and steel materials and iron oxide content in final slag are obviously reduced, dephosphorization efficiency is further improved, and the quality of molten steel at the end of smelting is obviously improved. A long-life bottom blowing element with directional multi-microporous structure has been developed, which has excellent air permeability, high temperature resistance, thermal shock resistance and impact resistance. In this technology, the subsection dynamic bottom blowing process model based on "melting-dephosphorization-decarbonization-heating-end point control" in EAF smelting is adopted, which not only improves the gas mixing efficiency, but also reduces the mechanical erosion and chemical erosion of gas-liquid mixed pulsating fluid to bottom blowing elements. By monitoring the flow rate, pressure and temperature of bottom blowing, the whole process alarm of multi-point, step and section is realized, and the arc-shaped anti-seepage structure design is adopted to ensure the bottom structure safety of the electric arc furnace. Industrial practice shows that the bottom blowing life of EAF is over 800 times, which is synchronized with the furnace life.
Dynamic bottom blowing technology of arc furnace CO2-Ar.
Based on the technology of safe and long life bottom blowing in electric arc furnace, and based on the physical and chemical characteristics of CO2 and CO2 reaction mechanism in high temperature metallurgical molten pool, the team invented the dynamic bottom blowing technology and equipment system of CO 2-Ar in electric arc furnace. They explored the mechanism of denitrification by CO 2-Ar multi-medium bubbles in metal molten pools and found that the reaction rate of denitrification by bottom blowing CO 2 was nearly 10 times higher than that by Ar. A mathematical model of stirring energy density of molten steel under the conditions of bottom blowing Ar and CO2 in electric arc furnace was established. It was found that the stirring capacity of bottom blowing CO 2 was obviously greater than that of bottom blowing Ar, and the furnace structure of flat shallow molten pool was also established. Under these conditions, the bottom blowing of CO2 in EAF can further enhance the stirring of the molten pool, uniform composition and temperature. Industrial production data show that compared with bottom blowing Ar, the nitrogen content of liquid steel at the end point of EAF smelting is stabilized below 45 *10-6 and the cleanliness of molten steel is further improved after adopting dynamic bottom blowing technology of CO 2-Ar in EAF. At the same time, based on the reaction absorption/exothermic principle of CO 2 and molten steel elements, the team invented the control method of CO 2 injection to improve the service life of bottom blowing permeable bricks in EAF. By dynamically controlling the ratio and flow rate of bottom blowing Ar and CO 2, the erosion speed of bottom blowing elements was further reduced and the service life of bottom blowing was prolonged.
A new gas-solid injection technology for EAF steelmaking.
On the basis of traditional wall powder injection and embedded oxygen injection technology, the team proposed and developed new gas-solid injection smelting technology in arc furnace pool, including rapid deep dephosphorization by O 2-CaO injection and carbon powder injection. The technology uses spraying gun (buried under the molten steel level) to spray lime powder or carbon powder directly into the molten pool of electric arc furnace, realizing rapid and clean steelmaking in electric arc furnace, and improving the quality of molten steel. This technology moves the traditional powder spraying method above the molten pool to the bottom of the molten pool, showing obvious technical advantages in production efficiency, technical indicators, steel quality and so on.
The technology of rapid deep dephosphorization by O 2-CaO injection in molten pool, using O 2 or O 2-CO 2 to spray lime powder into the molten pool, and relying on the "gas-solid-slag-gold" multiphase reaction system in the molten pool, realizes rapid deep dephosphorization in electric arc furnace steelmaking. This technology has changed the traditional dephosphorization method in EAF steelmaking, and provided a new efficient dephosphorization method in EAF steelmaking. It uses the micro-system of molten slag particles to quickly and deeply dephosphorize, which improves the dephosphorization efficiency and improves the quality of molten steel.
Safety and longevity bottom blowing technology for EAF steelmaking.
The metallurgical reaction kinetics of EAF steelmaking pool is poor, the composition and temperature of molten steel in the pool are not uniform, the oxygen content at the end point and the iron oxide content in slag are high, which ultimately affect the smelting index and the quality of molten steel. The safe and long life bottom blowing technology of EAF steelmaking developed by the team strengthens the stirring of EAF melting pool. Oxygen consumption per ton of steel, consumption of iron and steel materials and iron oxide content in final slag are obviously reduced, dephosphorization efficiency is further improved, and the quality of molten steel at the end of smelting is obviously improved. A long-life bottom blowing element with directional multi-microporous structure has been developed, which has excellent air permeability, high temperature resistance, thermal shock resistance and impact resistance. In this technology, the subsection dynamic bottom blowing process model based on "melting-dephosphorization-decarbonization-heating-end point control" in EAF smelting is adopted, which not only improves the gas mixing efficiency, but also reduces the mechanical erosion and chemical erosion of gas-liquid mixed pulsating fluid to bottom blowing elements. By monitoring the flow rate, pressure and temperature of bottom blowing, the whole process alarm of multi-point, step and section is realized, and the arc-shaped anti-seepage structure design is adopted to ensure the bottom structure safety of the electric arc furnace. Industrial practice shows that the bottom blowing life of EAF is over 800 times, which is synchronized with the furnace life.
Dynamic bottom blowing technology of arc furnace CO2-Ar.
Based on the technology of safe and long life bottom blowing in electric arc furnace, and based on the physical and chemical characteristics of CO2 and CO2 reaction mechanism in high temperature metallurgical molten pool, the team invented the dynamic bottom blowing technology and equipment system of CO 2-Ar in electric arc furnace. They explored the mechanism of denitrification by CO 2-Ar multi-medium bubbles in metal molten pools and found that the reaction rate of denitrification by bottom blowing CO 2 was nearly 10 times higher than that by Ar. A mathematical model of stirring energy density of molten steel under the conditions of bottom blowing Ar and CO2 in electric arc furnace was established. It was found that the stirring capacity of bottom blowing CO 2 was obviously greater than that of bottom blowing Ar, and the furnace structure of flat shallow molten pool was also established. Under these conditions, the bottom blowing of CO2 in EAF can further enhance the stirring of the molten pool, uniform composition and temperature. Industrial production data show that compared with bottom blowing Ar, the nitrogen content of liquid steel at the end point of EAF smelting is stabilized below 45 *10-6 and the cleanliness of molten steel is further improved after adopting dynamic bottom blowing technology of CO 2-Ar in EAF. At the same time, based on the reaction absorption/exothermic principle of CO 2 and molten steel elements, the team invented the control method of CO 2 injection to improve the service life of bottom blowing permeable bricks in EAF. By dynamically controlling the ratio and flow rate of bottom blowing Ar and CO 2, the erosion speed of bottom blowing elements was further reduced and the service life of bottom blowing was prolonged.
A new gas-solid injection technology for EAF steelmaking.
On the basis of traditional wall powder injection and embedded oxygen injection technology, the team proposed and developed new gas-solid injection smelting technology in arc furnace pool, including rapid deep dephosphorization by O 2-CaO injection and carbon powder injection. The technology uses spraying gun (buried under the molten steel level) to spray lime powder or carbon powder directly into the molten pool of electric arc furnace, realizing rapid and clean steelmaking in electric arc furnace, and improving the quality of molten steel. This technology moves the traditional powder spraying method above the molten pool to the bottom of the molten pool, showing obvious technical advantages in production efficiency, technical indicators, steel quality and so on.
The technology of rapid deep dephosphorization by O 2-CaO injection in molten pool, using O 2 or O 2-CO 2 to spray lime powder into the molten pool, and relying on the "gas-solid-slag-gold" multiphase reaction system in the molten pool, realizes rapid deep dephosphorization in electric arc furnace steelmaking. This technology has changed the traditional dephosphorization method in EAF steelmaking, and provided a new efficient dephosphorization method in EAF steelmaking. It uses the micro-system of molten slag particles to quickly and deeply dephosphorize, which improves the dephosphorization efficiency and improves the quality of molten steel.
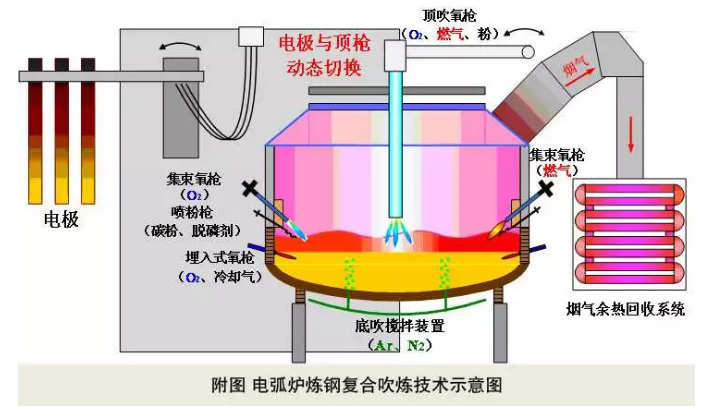
Carbon powder injection technology in molten pool can accelerate carburization of molten steel by spraying carbon powder into molten pool by air or CO2-O2, promote the melting of scrap steel, increase the carbon content of molten steel and improve the quality of molten steel. The technology directly injected carbon powder into the molten steel, avoiding the oxidation of carbon and the high temperature flue gas and slag in the furnace, and significantly increased the utilization efficiency of the carbon powder. A good pool stirring accelerated the dispersion of the carbon powder in the molten steel, and increased the carburizing efficiency of the molten pool. It consumes electricity and electrodes.
The quality analysis, monitoring and cost control system of electric arc furnace steelmaking.
With the development of electric arc furnace (EAF) smelting technology, it is impossible to control EAF production by relying solely on the operator's experience to adapt to the production rhythm of modern EAF steelmaking. Through the exchange of data and information and process optimization control, the cost control and reasonable energy supply of EAF steelmaking process can be optimized, cost reduction and efficiency can be improved. The quality analysis, monitoring and cost control system of EAF steelmaking based on this development has the following characteristics: First, through the analysis of EAF-LF steelmaking process end-point component control model, EAF-LF steelmaking process component data are analyzed, and the parameters of component control relationship are dynamically adjusted to predict the real-time oxygen content and alloy element yield and guide deoxidation. The EAF-LF steelmaking process can be accurately controlled by process and alloy feeding process. The second is to establish the history database of EAF smelting process. According to the principle of lowest cost, lowest energy consumption or shortest smelting time, the optimal historical data similar to the current burden structure and smelting environment are selected, and then the smelting process is carried out according to the optimal number of smelting processes to achieve the optimal smelting effect. Thirdly, the cost monitoring system of electric arc furnace and refining process has been established to predict and calculate the cost of single furnace of electric arc furnace in real time, and to provide guidance curves and optimization of power supply and oxygen supply for different burden structures; to predict and calculate the cost of single furnace of refining furnace in real time, and to provide optimized alloy and slag combination. At present, the system has been widely used in many electric arc furnaces at home and abroad.
The quality analysis, monitoring and cost control system of electric arc furnace steelmaking.
With the development of electric arc furnace (EAF) smelting technology, it is impossible to control EAF production by relying solely on the operator's experience to adapt to the production rhythm of modern EAF steelmaking. Through the exchange of data and information and process optimization control, the cost control and reasonable energy supply of EAF steelmaking process can be optimized, cost reduction and efficiency can be improved. The quality analysis, monitoring and cost control system of EAF steelmaking based on this development has the following characteristics: First, through the analysis of EAF-LF steelmaking process end-point component control model, EAF-LF steelmaking process component data are analyzed, and the parameters of component control relationship are dynamically adjusted to predict the real-time oxygen content and alloy element yield and guide deoxidation. The EAF-LF steelmaking process can be accurately controlled by process and alloy feeding process. The second is to establish the history database of EAF smelting process. According to the principle of lowest cost, lowest energy consumption or shortest smelting time, the optimal historical data similar to the current burden structure and smelting environment are selected, and then the smelting process is carried out according to the optimal number of smelting processes to achieve the optimal smelting effect. Thirdly, the cost monitoring system of electric arc furnace and refining process has been established to predict and calculate the cost of single furnace of electric arc furnace in real time, and to provide guidance curves and optimization of power supply and oxygen supply for different burden structures; to predict and calculate the cost of single furnace of refining furnace in real time, and to provide optimized alloy and slag combination. At present, the system has been widely used in many electric arc furnaces at home and abroad.
Huachang company specialized in metallurgical equipment, industrial furnace development and manufacturing project construction comprehensive service providers, to provide one-stop professional services!
If you are looking for related products or have any other problems, you can call the company service hotline at any time, or click the button below to communicate with us online!
Customer Service Hotline
:086-88864421